Drying Solutions for Compressed Air Systems
Moisture in the form of condensate in compressed air systems creates a permanent danger for operation processes. Our DRYPOINT® RA and DRYPOINT® X compressed air dryers provide you with considerably increased process safety and therefore significant advantages - and go even one step further: Given their large energy-saving potential, you can also protect your financial resources and therefore utilize them more efficiently for your core business. An important criteria for the selection of a compressed air dryer is the desired degree of drying, the air volume flow rate, and the required air quality class.
DRYPOINT® RA Non-cycling Refrigerant Dryers
Refrigerant air dryers are commonly found in the majority of general industrial plant air applications. They offer users the best price-to-performance ratio in comparison to the compressed air quality produced. While the treated air may not be as dry as can be achieved with desiccant or membrane dryer technologies like DRYPOINT® X and DRYPOINT® M, the dry outlet air from refrigerant dryers is more than acceptable for the majority of applications.
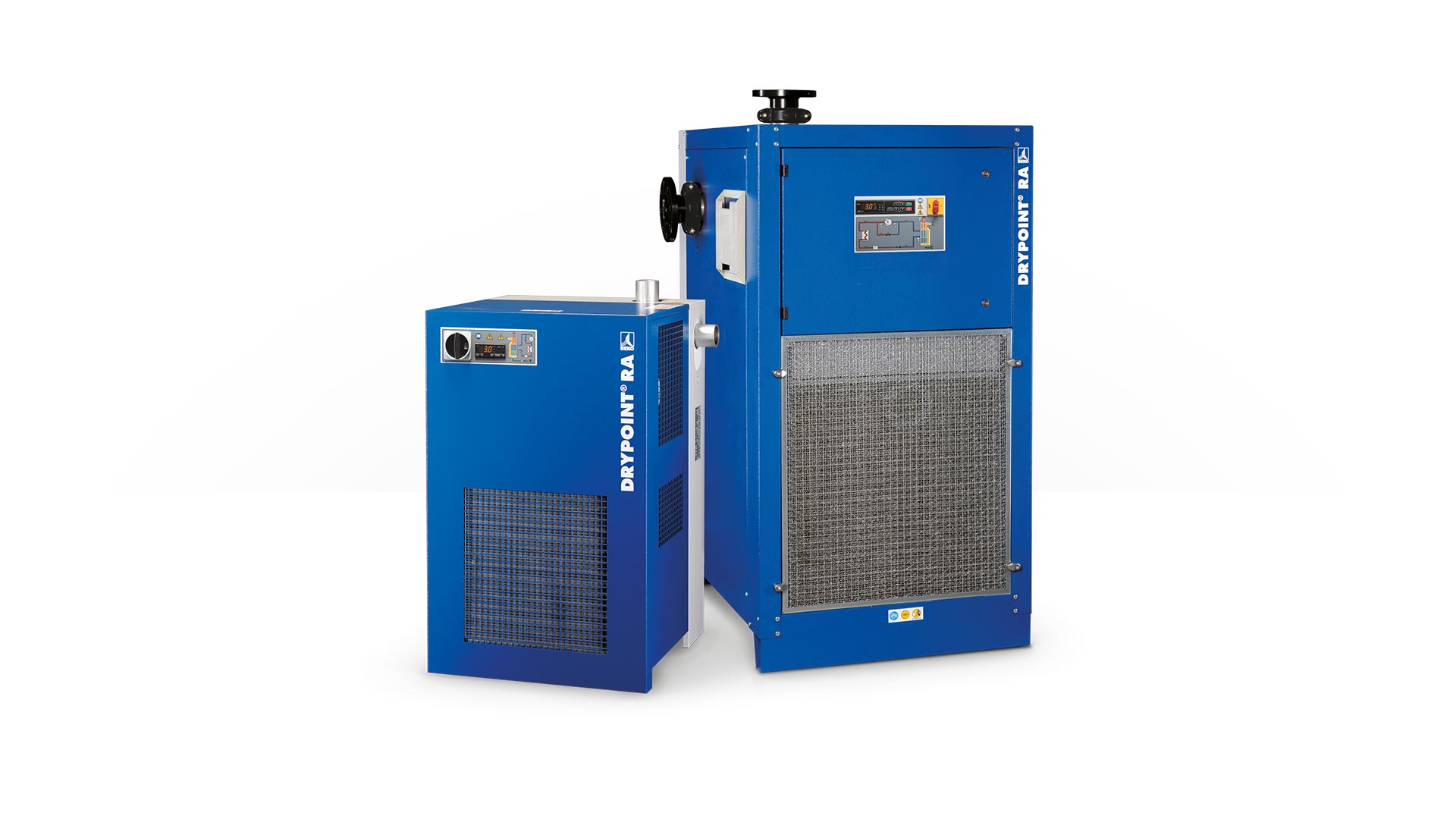
DRYPOINT® RA Energy Saving Refrigerant Dryers
Refrigerant air dryers are commonly found in the majority of general industrial plant air applications. They offer users the best price-to-performance ratio in comparison to the air quality produced. The dryness of the air may not be as low as with other dryer types, yet the outlet air from refrigerant dryers is more than acceptable for the majority of application. Specifically with the DRYPOINT® RA Eco Series dryers, users are provided with maximum energy savings from the cycling and variable speed technologies used.
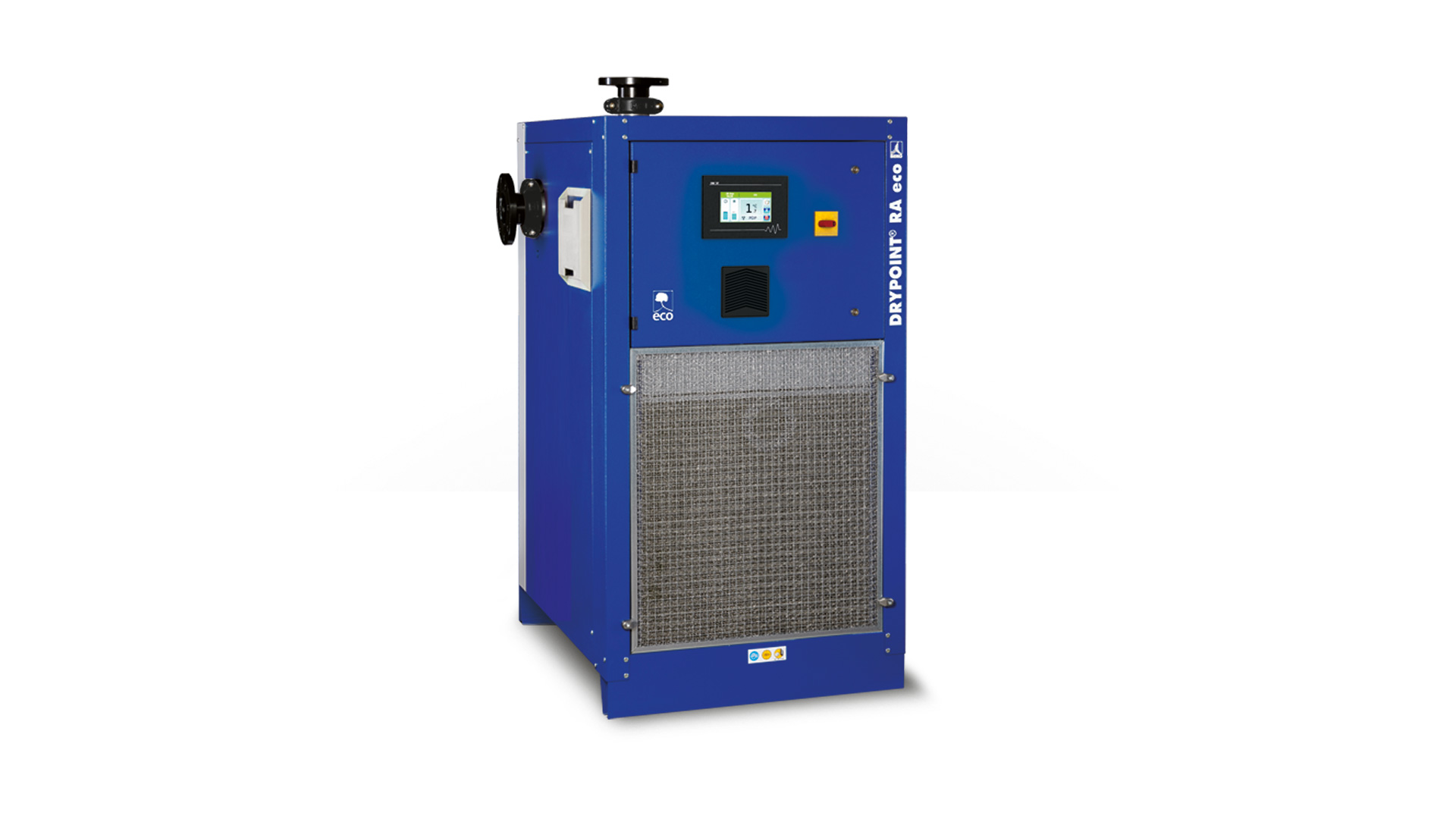
DRYPOINT® XC Heatless Desiccant Dryers
Regenerative desiccant dryers are frequently found in industrial applications around the world. These dryers use a desiccant material, which adsorbs the water vapor in the air stream. Heatless desiccant dryers utilize a small amount of dried air to regenerate the desiccant in one tower while the other tower dries the compressed air. DRYPOINT® XC Series heatless desiccant dryers provide very low dew points, are designed around reducing energy and process waste, and provide a very user friendly interface.
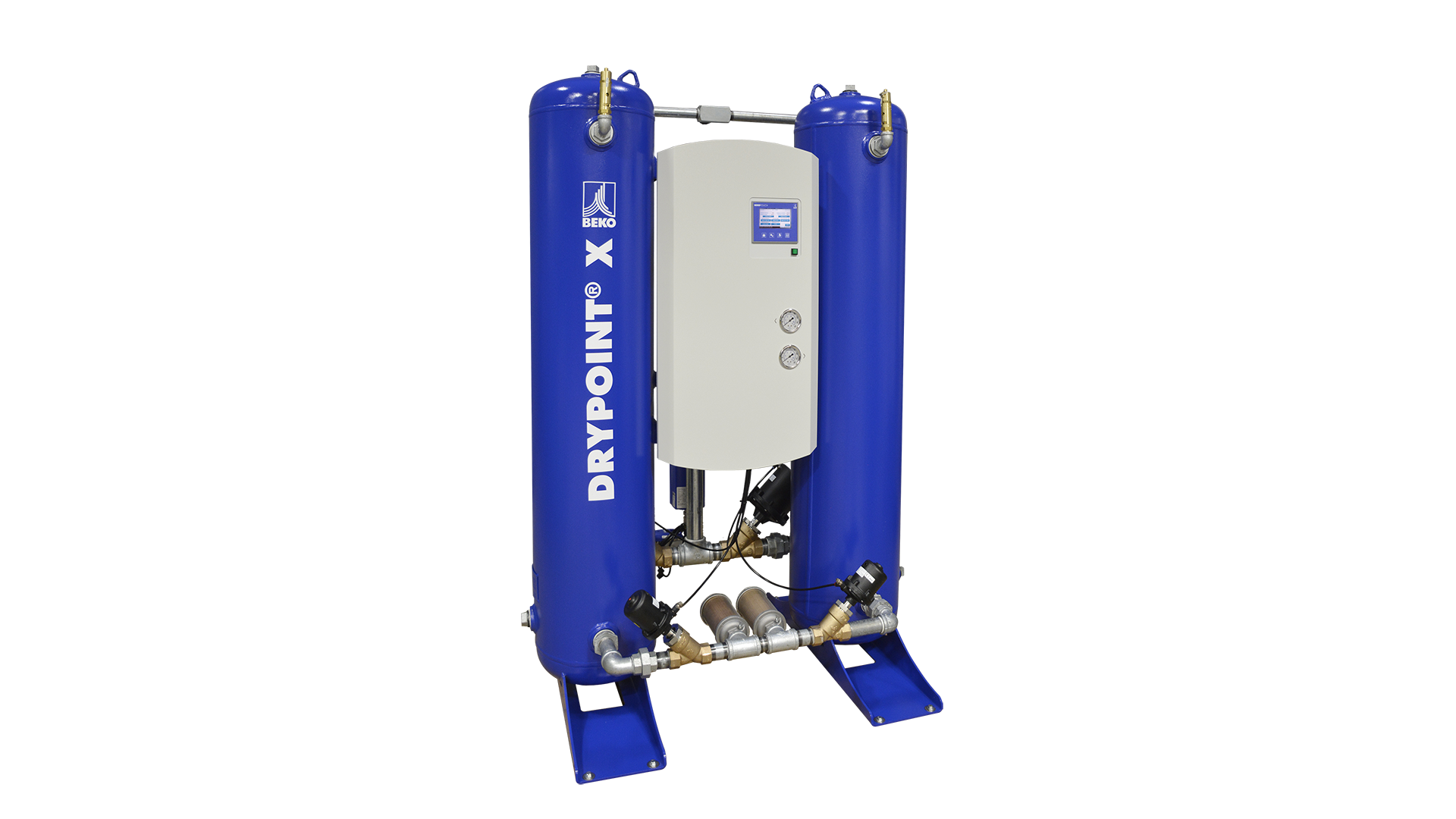
DRYPOINT® XF Heated Desiccant Dryers
Regenerative desiccant dryers are frequently found in industrial applications around the world. These dryers use a desiccant material, which adsorbs the water vapor in the air stream. Heated regenerative type desiccant dryers utilize an external heater to regenerate the desiccant in one tower while the other tower dries the compressed air to a very low dew point. The DRYPOINT® XFi models use patented, hyper-intelligent technology and autonomous systems to control the performance and maximize cost savings.
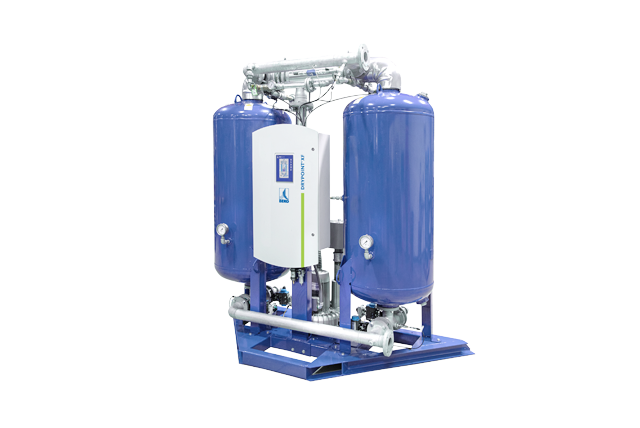
DRYPOINT® XH Heated Purge Desiccant Dryers
Regenerative desiccant dryers are frequently found in industrial applications around the world. These dryers use a desiccant material, which adsorbs the water vapor in the air stream. Heated regenerative type desiccant dryers utilize an external heater to regenerate the desiccant in one tower while the other tower dries the compressed air to a very low dew point. The DRYPOINT XHi models use a patent-pending, intelligent algorithm and systems to control the performance and maximize cost savings.
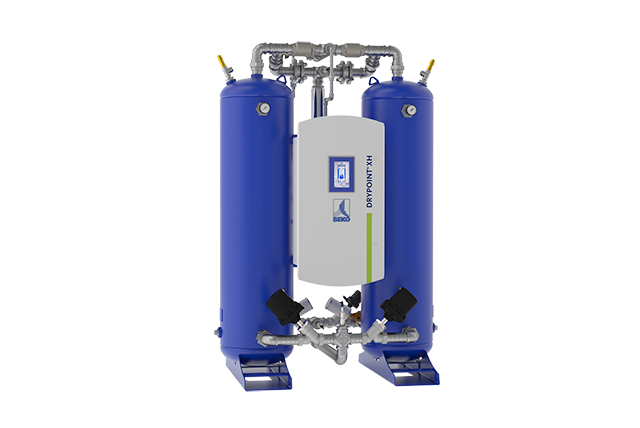
DRYPOINT® MD Membrane Dryers
Membrane air dryers are a type of dryer that use permeable fiber technology and the process of de-humidification to dry compressed air streams to the required dew point of an application. The Compressed Air and Gas Institute advises us to dry only the compressed air that is actually being used, and to make it only as dry as the application truly requires. Membrane air dryers are perfectly suited for this type of point-of-use drying, are adaptable to various ambient conditions, and require no electricity.
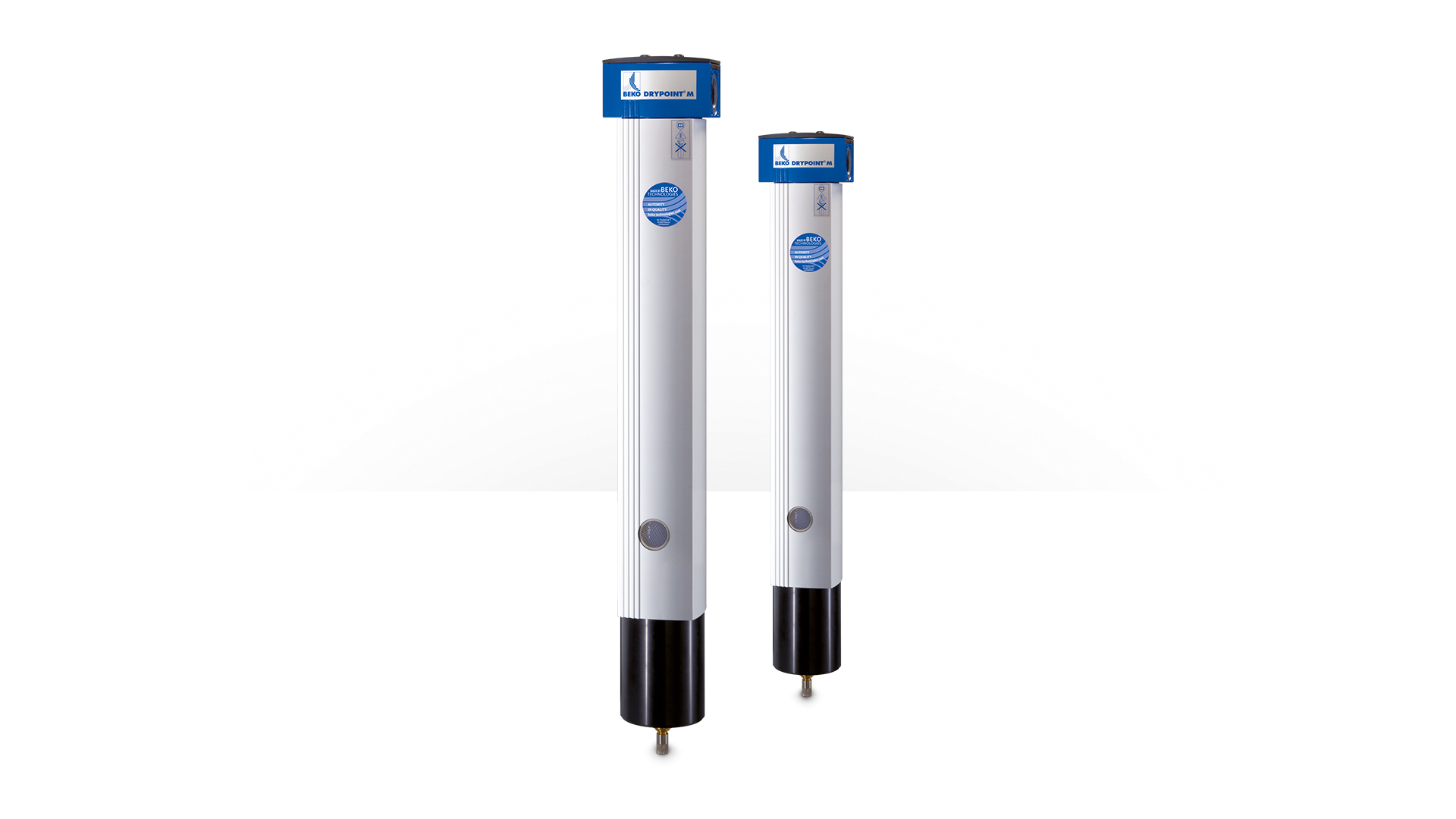