Tools | Facts About Compressed Air
On the page below you find a selection of white papers and fact sheets that serve to give you a condensed but significant amount of information on various topics in the field of compressed air in just a short time. Our mantra of Truth in Compressed Air holds true with the information presented here where we want to objectively present the facts you need to know to further assist your decision making when it comes to choosing a relaible, trustworthy partner like BEKO TECHNOLOGIES. In addition, this knowledge base will be extended on a regular basis.
Topic Selection
Production of Oil-free Compressed Air
The ISO 8573 standard was created to provide an international standard for the quality of compressed air. Part 1 of the standard specifies the purity classes of compressed air.
One important aspect within the standard is contamination with oil, which includes all hydrocarbons with six or more carbons in the molecular chain. To meet the requirements for quality class 1, the oil content must be less than or equal to 0.01 mg of oil per cubic meter, or 35 cubic feet, of expanded compressed air. This oil content includes hydrocarbons in liquid, aerosol, or vapor form.
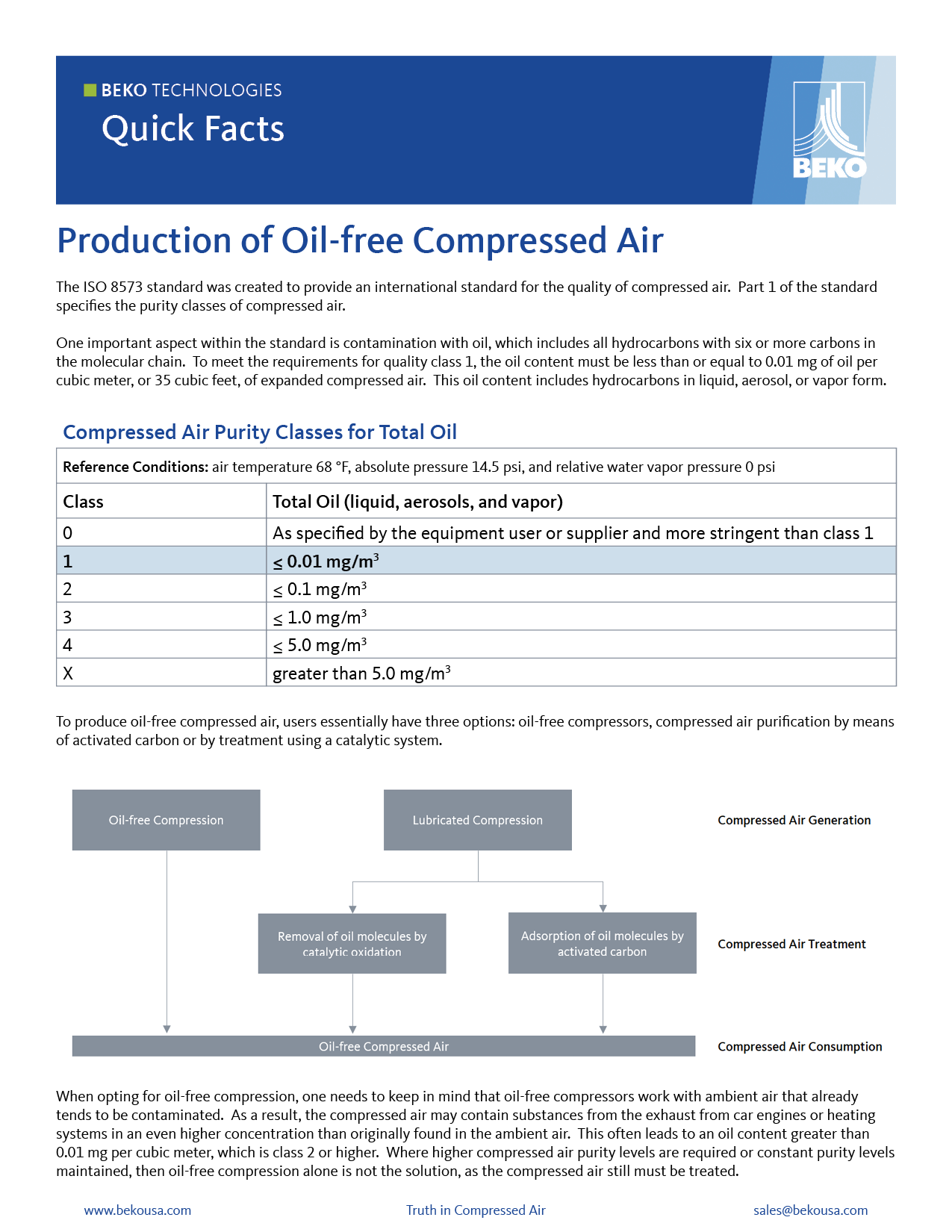
Production of oil-free compressed air with activated carbon and refrigeration drying
For the production of compressed air of ISO 8573 quality class 1, most operators use activated-carbon adsorbers that remove oil molecules from the compressed air by means of adsorption. As activated carbon also absorbs water vapour, it can be quickly spent, especially where the air contains quite a lot of water vapour. At this point, the activated-carbon adsorber is no longer able to take up oil molecules, so that the concentration in the downstream compressed air exceeds the limit for quality class 1 (> 0.01 mg/m3 ). For reliable long-term treatment and consistent low residual oil contents, the compressed air must therefore be dried before it enters the activated carbon...
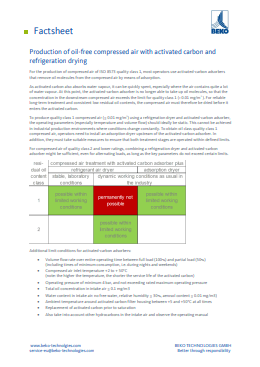
Preventive maintenance
Even high-quality compressed air system components are exposed to some wear. Preventive maintenance aimed at reducing the risk of failure or malfunction includes the timely replacement of wear and maintenance parts. Depending on the actual operation and the prevalent operating conditions, such parts should be replaced at least every 12 months.
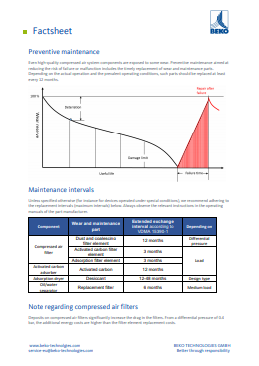
Calibration and adjustment
A measurement error is the difference between a measured value of quantity and its true value. Such errors tend to become more frequent the longer a device is in operation. At some time, the deviations might be so great that they are no longer within the specifications, which means that quality is no longer assured.
By calibrating the device, the measurement error can be determined and documented. If the measurements are outside the permissible range, the device needs to be adjusted. In this process, the measuring instrument is reconfigured so that measurement errors are minimised and deviations from the setpoint value are within the device specifications.
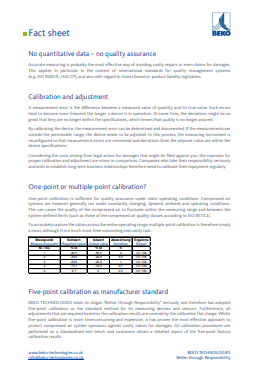
Optimising system pressure
An operating pressure that is too high by as little as 1 bar can already lead to a huge increase in operating costs.
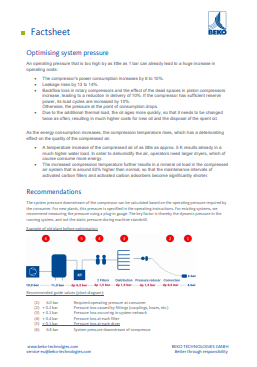
Compresssed air filters - The cost of pressure drop
Compressed air filters improve the quality of the compressed air by removing contaminants. As these tend to deposit on the filter material, the pressure drop increases gradually over time. To ensure that there is sufficient pressure available at the consumers, the compressor must compensate this pressure drop, which results in higher energy costs.
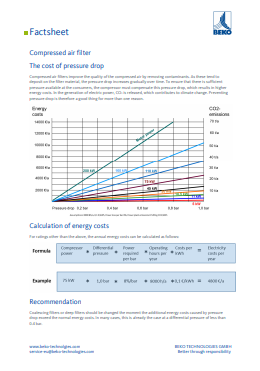